OEM Özel ve Çin'den Sfero Döküm Kum Döküm ŞirketiCNC İşleme Hizmetleri.
Dökme demir, pik demirin, hurdanın ve diğer ilavelerin yeniden eritilmesiyle elde edilen diğer elementlerle birlikte bir demir-karbon döküm alaşımıdır. Çelik ve dökme çelikten ayırmak için dökme demir, son fazın ötektik dönüşümle katılaşmasını sağlayan karbon içeriğine sahip (en az %2,03) bir dökme alaşım olarak tanımlanır.
Kimyasal özelliklerine bağlı olarak dökme demirler alaşımsız veya alaşımlı olabilir. Alaşımlı demirlerin aralığı çok daha geniştir ve ya silikon ve manganez gibi daha yüksek miktarlarda ortak bileşenler ya da nikel, krom, alüminyum, molibden, tungsten, bakır, vanadyum, titanyum gibi özel katkılar içerirler. diğerleri. Genel olarak dökme demir, gri demir, sfero demir (sfero demir), beyaz dökme demir, sıkıştırılmış grafit demir ve dövülebilir dökme demir olarak ayrılabilir.
Kabuk kalıplama döküm işlemiön kaplamalı reçineli kum döküm işlemi, sıcak kabuklu kalıplama dökümü veya maça döküm işlemi olarak da adlandırılır. Ana kalıplama malzemesi, yaş kum ve furan reçine kumundan daha pahalı olan, önceden kaplanmış fenolik reçine kumudur. Üstelik bu kum geri dönüştürülerek kullanılamaz.
Kabuk kalıplama demir döküm parçaları kum dökümüne göre daha yüksek maliyetlere sahiptir. Ancak,kabuk kalıplama döküm parçalarıdaha sıkı boyut toleransı, iyi yüzey kalitesi ve daha az döküm hatası gibi birçok avantaja sahiptir.
▶ Kabuk Kalıplama Döküm Hammaddeleri:
• Dökme Karbon Çelik: AISI 1020'den AISI 1060'a kadar Düşük Karbonlu Çelik, Orta Karbonlu Çelik ve Yüksek Karbonlu Çelik.
• Çelik Döküm Alaşımları: 20CrMnTi, 20SiMn, 30SiMn, 30CrMo, 35CrMo, 35SiMn, 35CrMnSi, 40Mn, 40Cr, 42Cr, 42CrMo...vb. istek üzerine.
• Paslanmaz Çelik Döküm: AISI 304, AISI 304L, AISI 316, AISI 316L ve diğer paslanmaz çelik kaliteleri.
• Dökme Alüminyum Alaşımları.
• Pirinç ve Bakır.
• Talep üzerine Diğer Malzemeler ve Standartlar
▶ Kabuk Döküm Kapasiteleri:
• Maksimum Boyut: 1.000 mm × 800 mm × 500 mm
• Ağırlık Aralığı: 0,5 kg - 100 kg
• Yıllık Kapasite: 2.000 ton
• Toleranslar: Talep Üzerine.
▶ Hassas Kabuk Kalıba Döküm Bileşenlerinin İncelenmesi:
• Spektrografik ve manuel kantitatif analiz
• Metalografik analiz
• Brinell, Rockwell ve Vickers sertlik denetimi
• Mekanik özellik analizi
• Düşük ve normal sıcaklıkta darbe testi
• Temizlik denetimi
• UT, MT ve RT denetimi
▶ Kabuk Kalıp Döküm İşlemleri:
✔ Metal Desenlerin Yapılması. Önceden kaplanmış reçine kumunun modellerde ısıtılması gerekir, bu nedenle metal modeller kabuk kalıplama dökümleri yapmak için gerekli aletlerdir.
✔ Ön Kaplamalı Kum Kalıbının Yapılması. Metal kalıpları kalıplama makinesine yerleştirdikten sonra, önceden kaplanmış reçine kumu kalıplara püskürtülecek ve ısıtıldıktan sonra reçine kaplama eriyecek, ardından kum kalıpları katı kum kabuğu ve çekirdekleri haline gelecektir.
✔ Dökme Metalin Eritilmesi. İndüksiyon fırınları kullanılarak malzemeler eritilerek sıvı hale getirilecek, daha sonra sıvı demirin kimyasal bileşimleri gerekli sayı ve yüzdelerle eşleşecek şekilde analiz edilmelidir.
✔ Metal Dökme. Erimiş demir gereksinimleri karşıladığında kabuk kalıplara dökülecektir. Döküm tasarımının farklı karakterlerine bağlı olarak, kabuk kalıplar yeşil kuma gömülecek veya katmanlar halinde istiflenecektir.
✔ Kumlama, Taşlama ve Temizleme. Dökümlerin soğutulması ve katılaşmasından sonra yükselticiler, kapılar veya ilave demirler kesilip çıkarılmalıdır. Daha sonra demir dökümler kumlama ekipmanı veya kumlama makineleri ile temizlenecektir. Yolluk kafasının ve ayırma hatlarının taşlanmasından sonra, bitmiş döküm parçaları gelir ve gerekirse sonraki işlemler beklenir.
▶ Shell Kalıp Döküm Bileşenleri için Neden RMC'yi Seçmelisiniz?
✔ Hassasiyet ve dolayısıyla yüksek malzeme kullanımı. Kabuk kalıplama dökümünden sonra net veya net şekle yakın ürünler elde edersiniz, son kullanıcıların gereksinimlerine bağlı olarak hiç işleme işlemi gerekmez veya çok az işlem gerekir.
✔ Daha iyi yüzey performansı. Kalıplamada kullanılan yeni teknoloji malzemeler sayesinde, kabuk kalıplamadan elde edilen dökümler çok daha ince ve daha yüksek doğrulukta bir yüzeye sahip olur.
✔ Kum dökümü ve yatırıma göre iyi dengeli bir seçim. Kabuk kalıplama dökümü, kum dökümüne göre daha iyi performansa ve yüzeye sahipken, hassas hassas dökümden çok daha düşük maliyetlere sahiptir.
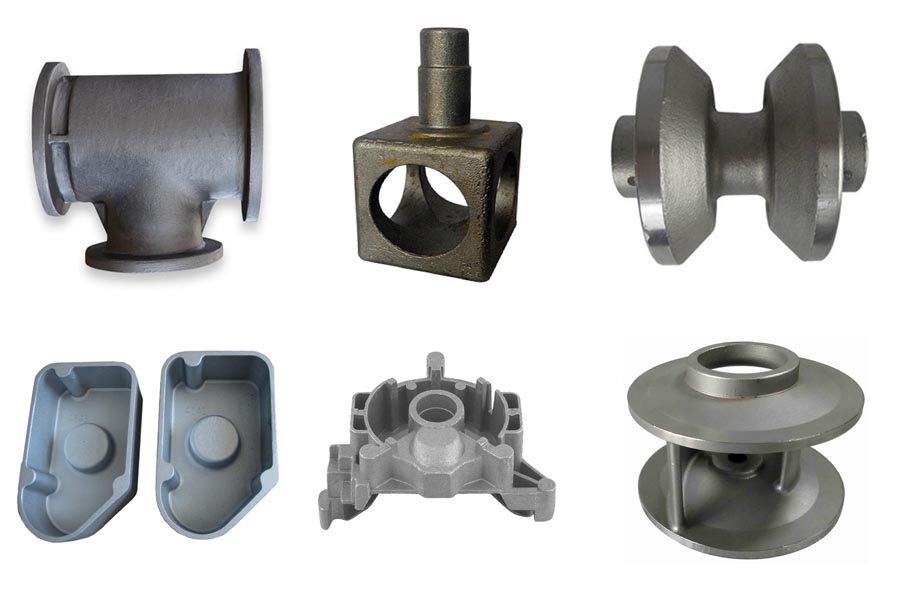