Kabuk kalıp dökümütermoset reçineyle karıştırılan kumun ısıtılmış metalik desen plakasıyla temas etmesine izin verildiği, böylece desen çevresinde ince ve güçlü bir kalıp kabuğunun oluşturulduğu bir işlemdir. Daha sonra kalıptan kabuk çıkarılır ve başlık ve kalama birlikte çıkarılır ve gerekli destek malzemesiyle birlikte bir şişede tutulur ve erimiş metal kalıba dökülür.
Kabuk kalıplama kumunun hazırlanmasında genellikle kilden tamamen arınmış kuru ve ince kum (90 ila 140 GFN) kullanılır. Seçilecek tane boyutu, dökümde istenen yüzey kalitesine bağlıdır. Çok ince tane boyutu, büyük miktarda reçine gerektirir, bu da kalıbı pahalı hale getirir.
Kabuk kalıplamada kullanılan sentetik reçineler esasen ısıyla geri dönüşü olmayacak şekilde sertleşen, ısıyla sertleşen reçinelerdir. En yaygın kullanılan reçineler fenol formaldehit reçineleridir. Kumla birleştiğinde çok yüksek mukavemete ve ısıya karşı dirence sahiptirler. Kabuk kalıplamada kullanılan fenolik reçineler genellikle iki aşamalı tiptedir, yani reçine fazla fenol içerir ve termoplastik bir malzeme gibi davranır. Kumla kaplama sırasında reçine, ısıyla sertleşme özelliklerini geliştirmek üzere yaklaşık %14 ila %16 oranında heksa metilen tetramin (heksa) gibi bir katalizörle birleştirilir. Bunlar için kürleme sıcaklığı 150 C civarında olacak ve gereken süre 50 ila 60 saniye olacaktır.
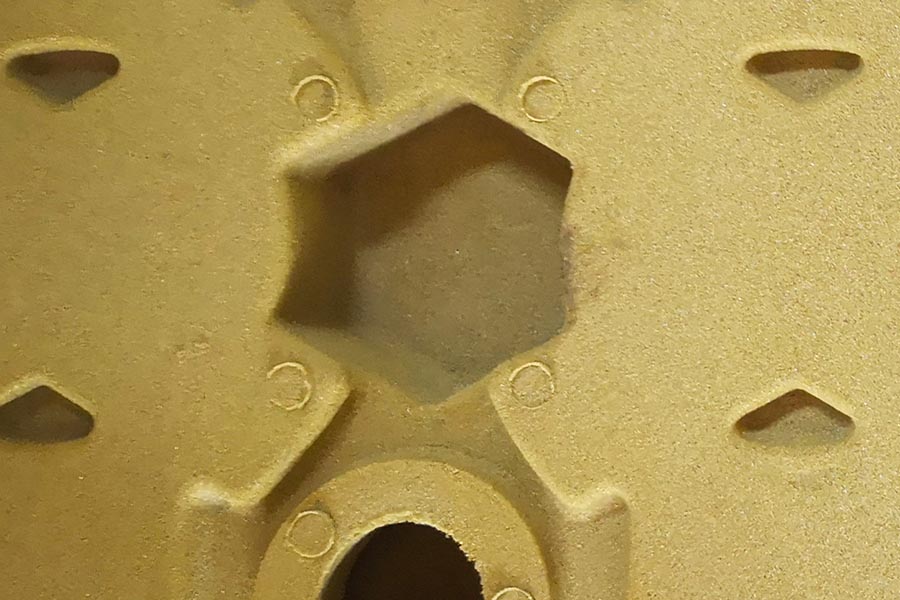
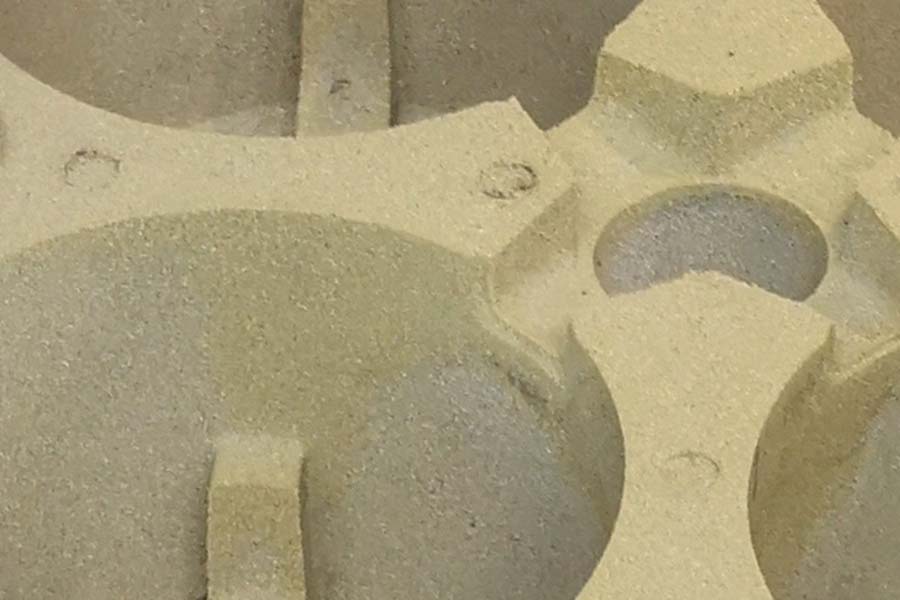
Shell Kalıp Döküm Prosesinin Avantajları
1.Kabuk-kalıp dökümlerigenellikle kum dökümlerine göre boyutsal olarak daha doğrudur. Çelik dökümlerde +0,25 mm, +0 tolerans elde etmek mümkündür. Gri dökme demir dökümler için 35 mm vesünek demir dökümlernormal çalışma koşulları altında. Dar toleranslı kabuk kalıpları durumunda, belirli uygulamalar için +0,03 ila +0,13 mm aralığında elde edilebilir.
2. Kabuk dökümlerde daha düzgün bir yüzey elde edilebilir. Bu öncelikle kullanılan daha ince tanecik boyutuyla elde edilir. Tipik pürüzlülük aralığı 3 ila 6 mikron arasındadır.
3. Daha düşük olan taslak açıları kum dökümleriKabuk kalıplarında gereklidir. Taslak açılarındaki azalma %50 ila %75 arasında olabilir, bu da malzeme maliyetlerinden ve sonraki işleme maliyetlerinden önemli ölçüde tasarruf sağlar.
4. Bazen kabuk kalıplamada özel çekirdekler ortadan kaldırılabilir. Kumun yüksek mukavemeti olduğundan kalıp, iç boşlukların doğrudan kabuk maçalarına ihtiyaç duyularak oluşturulabileceği şekilde tasarlanabilir.
5. Ayrıca, kalıplama için kullanılan kumun daha yüksek mukavemeti nedeniyle, hava soğutmalı silindir kafası tipinin çok ince bölümleri (0,25 mm'ye kadar) kabuk kalıplama ile kolaylıkla yapılabilir.
6. Kabuğun geçirgenliği yüksektir ve bu nedenle gaz kalıntıları oluşmaz.
7. Çok az miktarda kum kullanılması gerekmektedir.
8. Kabuk kalıplamada yer alan basit işlemler nedeniyle mekanizasyon kolaylıkla mümkündür.
Shell Kalıp Döküm Prosesinin Sınırlamaları
1. Modeller çok pahalıdır ve bu nedenle yalnızca büyük ölçekli üretimde kullanıldığında ekonomiktir. Tipik bir uygulamada, daha yüksek model maliyeti nedeniyle gerekli çıktı 15000 parçanın üzerindeyse kabuk kalıplama, kum kalıplamaya göre daha ekonomik hale gelir.
2. Kabuk kalıplamayla elde edilen dökümün boyutu sınırlıdır. Genellikle 200 kg ağırlığa kadar dökümler yapılabilmektedir, ancak daha küçük miktarlarda 450 kg ağırlığa kadar dökümler yapılmaktadır.
3. Çok karmaşık şekiller elde edilemez.
4. Isıtılmış metal modeller için gerekenler gibi kabuk kalıplarının taşınması için daha karmaşık ekipmanlara ihtiyaç vardır.
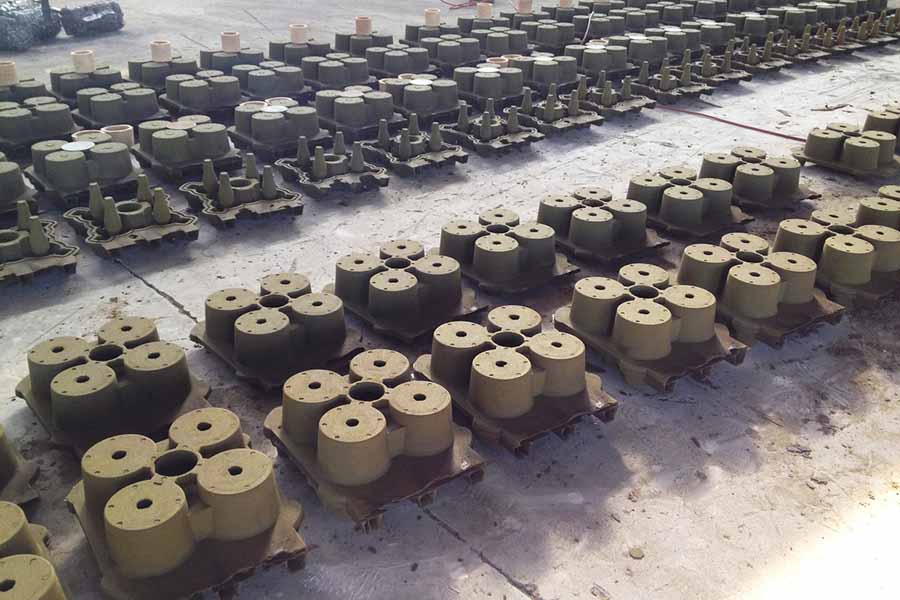
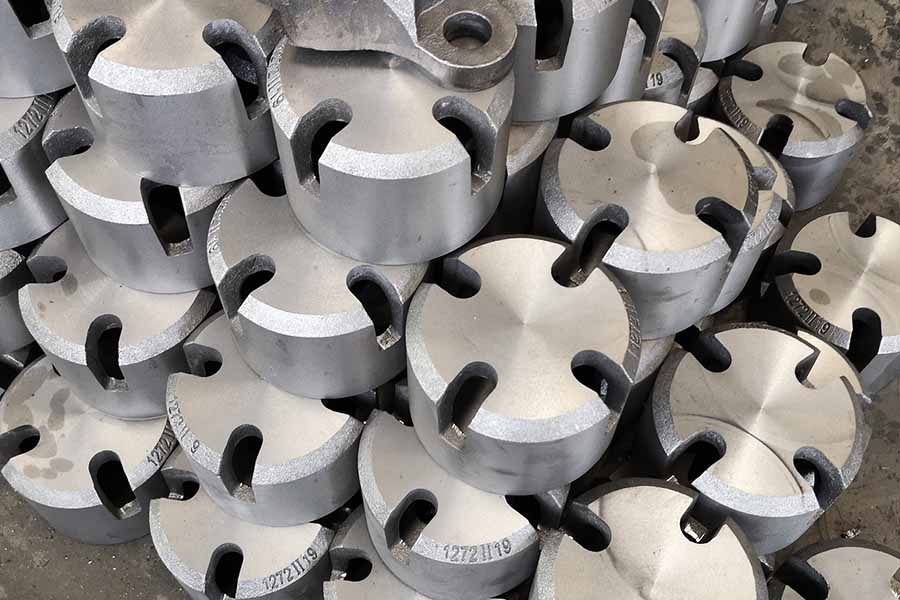
Gönderim zamanı: 25 Aralık 2020